Take control of your Food Production Facility with Proteus CMMS
Today’s food processing facilities are complex, highly automated, and highly regulated. While continuously making sure the production environment is safe, hygienic and efficient. In order to meet food safety and quality standards, you need a software solution that will help keep equipment operating at peak efficiency. A robust preventive maintenance scheduling module that generates work orders automatically so you will never miss scheduled maintenance.
Proteus MMX is a complete full-featured, integrated, Computerized Maintenance Management solution (CMMS) that provides the unique tools to run an efficient maintenance operation.

CMMS solutions to eliminate challenges
In general the need for improvement of some business elements is the main driver for a CMMS
Complex equipment to maintain
Maintaining highly automated packaging equipment
Compliance with Regulatory Standards
Using real-time Monitoring Key Performance Indicators (KPI’s) and Artificial Intelligent (AI) Reporting Chatbot like “Ask Steve” can allow executives to gain better insight on how the facility maintains its assets.

Benefits of a CMMS
Based on our experience with food facilities clear benefits can be seen after implementing
Proteus CMMS, more than half our customers reported:
Improved business intelligence with Key Performance Indicators and AI reporting
Improvements in equipment reliability
Improved cost controls
Improved spare parts control
Reduction in labor costs
Improvements in equipment availability
Reduction in materials costs
Reduction in other costs
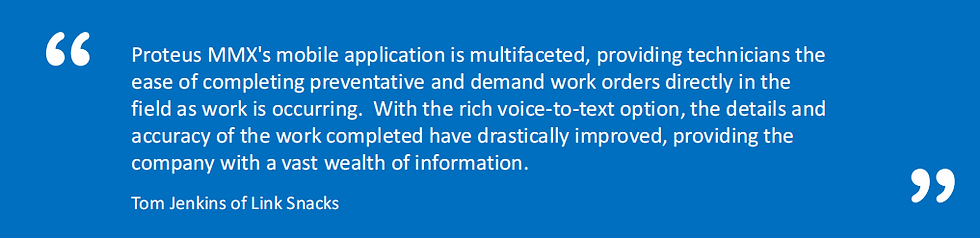
Manage Various Assets within one system
Food processing facilities have very important assets, from inventory, processing equipment and various buildings / facilities. . By using a CMMS, facility managers can reduce labor and energy costs, manage inventory, optimize asset performance and longevity, and insure safety.
Total Productive Maintenance (TPM)
Proteus MMX will manage, capture, and track inspection, maintenance and repair activities for cost
containment, and risk reduction. When you combine a Proteus MMX with Total Productive Maintenance (TPM), you can eliminate costly machine downtime and shift to preventive maintenance.
Predictive Maintenance
Proteus MMX integrated with machine monitoring systems provide a live and interactive tool with
insight into operational trends, identify pain points, and even indicate potential problems over time. This type of predictive maintenance can lead to even greater operational efficiency.
Proteus MMX Features
Asset profile management
Compile accurate information on equipment to analyze performance, meet audit requirements, schedule preventive maintenance, and reduce capital expenses. You can also group equipment under predefined classifications such as Repetitive or Job Shop.

Barcoding and data collection
Barcoding/QR coding makes it easy to label and track equipment, inventory, employees and work orders. Users can scan equipment to retrieve work order history, current work orders, add parts to work orders, bills of material, and attach pictures to communicate issues at the job source.
Regulatory Compliance
Maintenance records play a large part in compliance and reporting requirements from the Environmental Protection Agency (EPA) and the Occupational Safety and Health Administration (OSHA).
Tracking maintenance activities with Proteus CMMS software helps with regulatory inspections and ISO certification. In addition, track changes with audit trail module. Comprehensive performance and management reports are also available with Proteus CMMS software.
Mobile Asset tracking
One database for all asset information allows for easy retrieval, input on activities, parts usage,
and maintenance. RFID can be used to ensure information is always up to date on mobile
assets from lifts to grinders based on their location at the time work is to be performed.
Connected Enterprise and Integration
Systems integrations can provide additional functionality and eliminate redundant processes.
Proteus Alarm Interface (PAI) provides continuous alarm monitoring via a direct interface to Building Automation Systems (BAS) such as Tridium, Honeywell, Trane, Johnson Controls, Siemens, Schneider and many more!
PAI automatically issues work orders based on alarms, events or equipment runtimes. The work
orders define specific tasks and parts required to complete the job quickly and efficiently. Work
orders may be sent via e-mail, printer or sent directly to a technician’s mobile device,
informing them of alarm status and actions.
For connected enterprise, we offer integrations with popular Enterprise Resource Planning (ERP)
systems such as, SAP, Oracle, Microsoft Dynamics etc.
Budget Module
In addition to helping you track your expenses, Proteus MMX assist with managing budgets.
Contractor Management
Record maintenance activities completed by your service providers, compile equipment histories. Manage contractor quality control.
Key Performance Indicators (KPIs)
With real-time data dashboard, food processing facility assets can be monitored by the maintenance team to quickly identify potential problems. You can set KPI’s to monitor critical
issues for your organization to ensure you are compliant with regulatory requirements. KPIs
are also available for performance monitoring and management information.
Mobile
Record and track equipment with mobile and barcoding/QR technology for accurate, efficient,
and effective deployment. Use Proteus MMX mobile to create new, receive and close work
orders on your iOS, Windows 10, or Android® based phone/tablet device.

Microsoft Windows Mobile is a registered trademark of
Microsoft Corporation. iOS is a registered trademark of
Apple, Inc. Android is a trademark of GoogleInc.
Security and Risk management
It is vital for food processing plants to meet International Regulation Agencies requirements, as well as state and federal health requirements as expected to avoid liability claims, and comply with regulatory requirements.
Proteus MMX allows for;
Gathering of maintenance histories
Scheduling and performing preventive maintenance tasks
Managing and monitoring Assets and inventory
Performing Inspections
Implementing user levels of access and rights in Proteus MMX
Better risk management
User-specific accounts
Track all record changes, altered fields, value changes, date and time of the change, and whether the change is a data insertion, update, or deletion.
Warranty management
Plan ahead, receive notification on warranty expiration dates coming due.
Inspection
Document and protect inspection procedures on each piece of equipment and initiate inspections
based on time, equipment performance, or previous work ensuring equipment such as Elevated Bridges to meet the safest condition possible.
About us
The increased efficiency and effectiveness of maintenance operations, as well as the
reduction in repair, labor, and energy costs make adding Proteus CMMS to your food processing facilities maintenance team an easy decision.
For over 30 years, Eagle Technology, Inc. has been developing Enterprise Asset Management (EAM) and Computerized Maintenance Management Systems (CMMS) that are flexible and meet customer needs.
Our team of professionals are available to you, providing on-going support, training and consultation services, making sure you get the most out of your investment. We are available to teach best practices, 5-S (Sort, Set In Order, Shine, Standardize and Sustain), and we offer project management and turnkey implementation.







Due to customer confidentiality agreements not all customers are displayed, for more information please contact us.

Contact Us
Not sure if Proteus MMX from Eagle is for you? One of our Food and Beverage maintenance experts will gladly advise you on the best solution for your facility’s unique needs and compliance requirements, as well as assist in the plan to go from firefighting to preventive and predictive maintenance.


Millennium Insights
Phone: +61 3 9653 9341
Website: www.millenniuminsight.com

Comentarios